Manufacturing Process
- STEP01
Design/Programming
- >
- STEP02
Laser Cutting
- >
- STEP03
Bending
- >
- STEP04
Welding/Alignment
- >
- STEP05
Machining
- >
- STEP06
Painting/Plating/Printing
- >
- STEP07
Product Assembly
- >
- STEP08
Quality Inspection
01 Design/Programming
- Blueprint Analysis and Product Drawing
- Product Design Using Programs
- Process Analysis and Equipment Selection
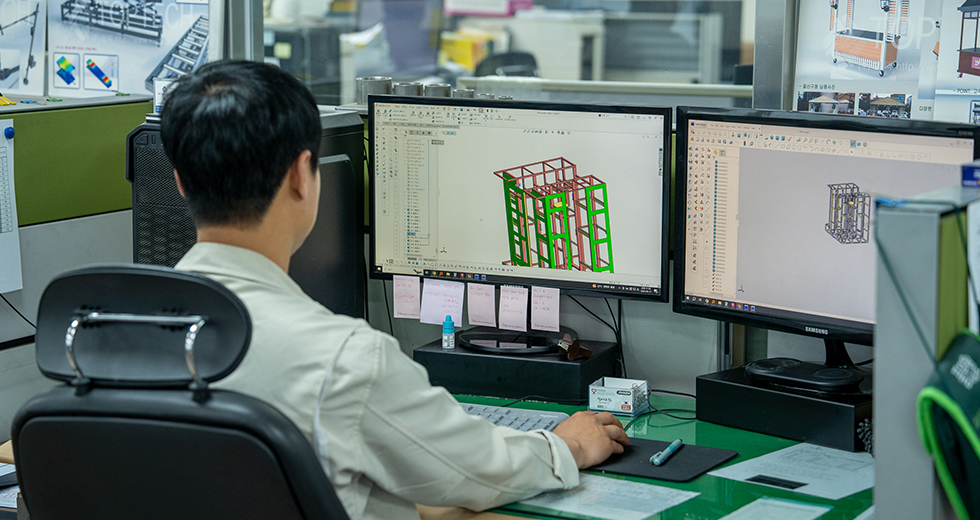
- Using a laser beam for cutting allows for easy processing of various shapes, resulting in smooth surfaces with no burrs.
- To generate the laser beam, liquefied nitrogen or liquefied carbon dioxide is used, depending on the material properties.
- Equipment Inventory : TruLaser Tube 7000, TruLaser 5030, TruLaser 3030
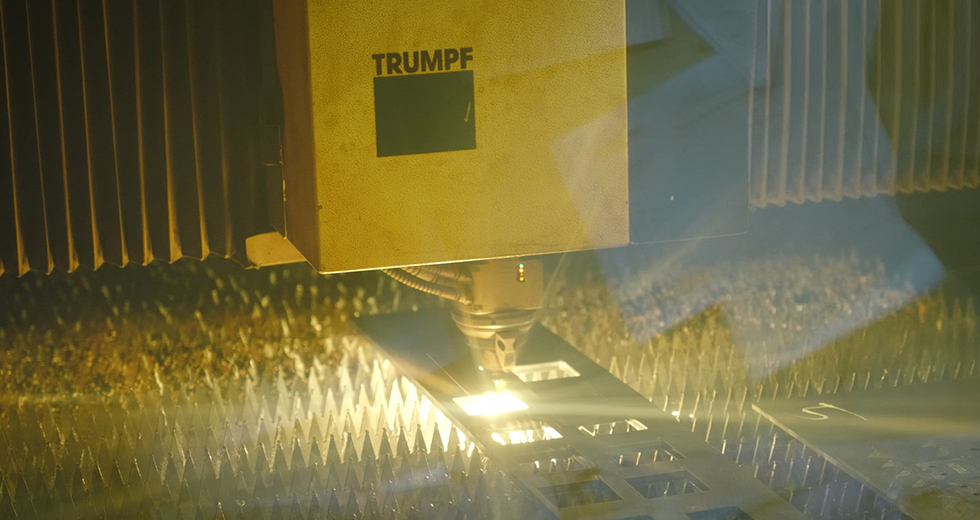
- A process that transforms material cut into flat shapes into the final product shape according to the design drawings.
- Various tools are used depending on the type of material and the bending shape.
- Equipment Inventory : TruBEND 5170, TruBend 7036, RG-50
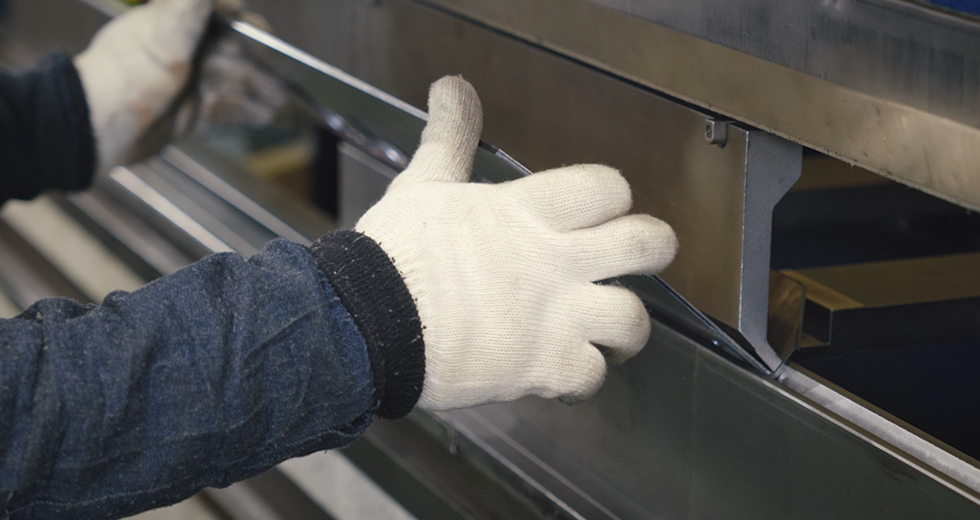
Welding
- A stage in which the product's shape is completed by welding and assembling joints, reinforcements, and other components.
- Depending on the product and material characteristics, various welding methods are used, including electric welding, TIG (argon) welding, CO2 welding, and spot welding.
Correction
- A process for correcting distortions in the material caused by high heat during welding. This requires devices and fixtures to prevent distortion.
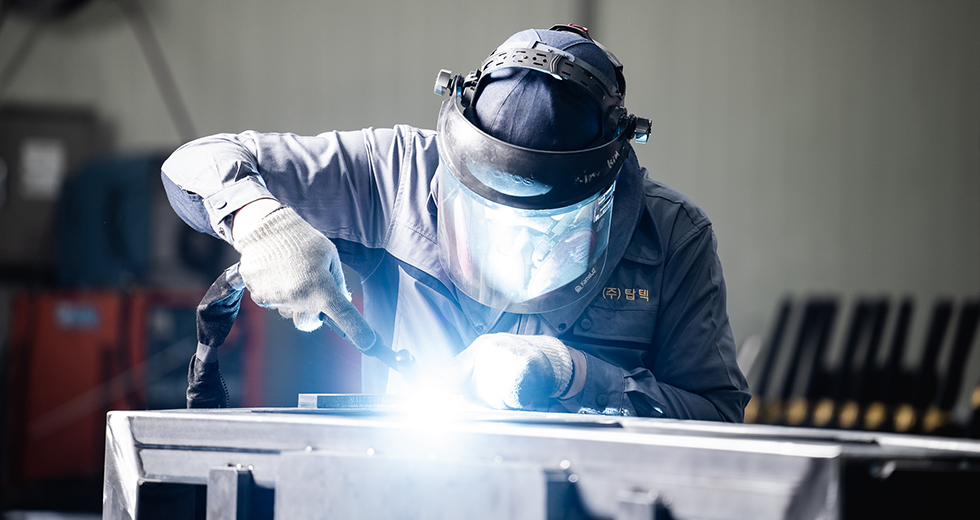
Painting
- Applied for corrosion resistance and to define the product's appearance.
- Depending on the product's use, both liquid and powder coatings are used.
Plating
- Applied for corrosion resistance and parts that require electrical conductivity.
- Types of plating include zinc, nickel, anodizing, and chromate, depending on the product material.
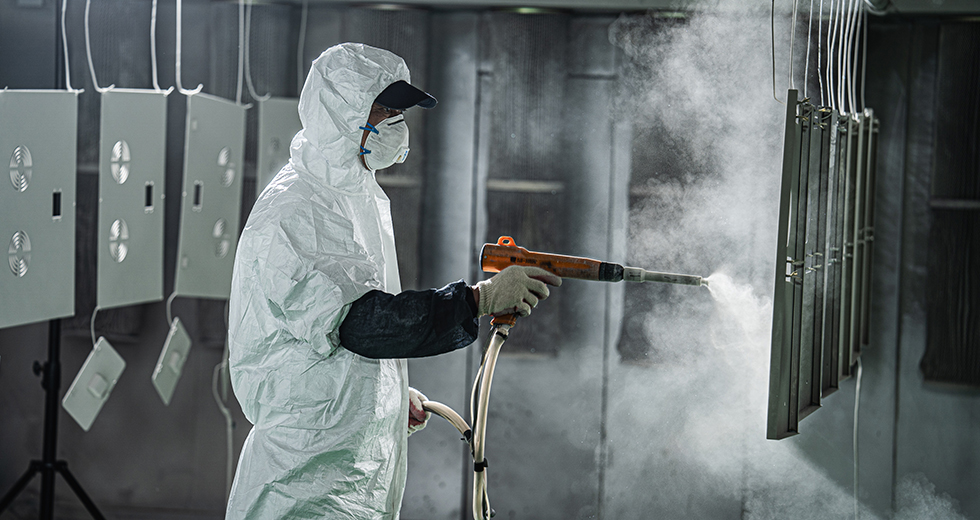
07 Product Assembly
- The process of completing the final assembly of the product.
(Assembling according to design drawings and customer specifications.)
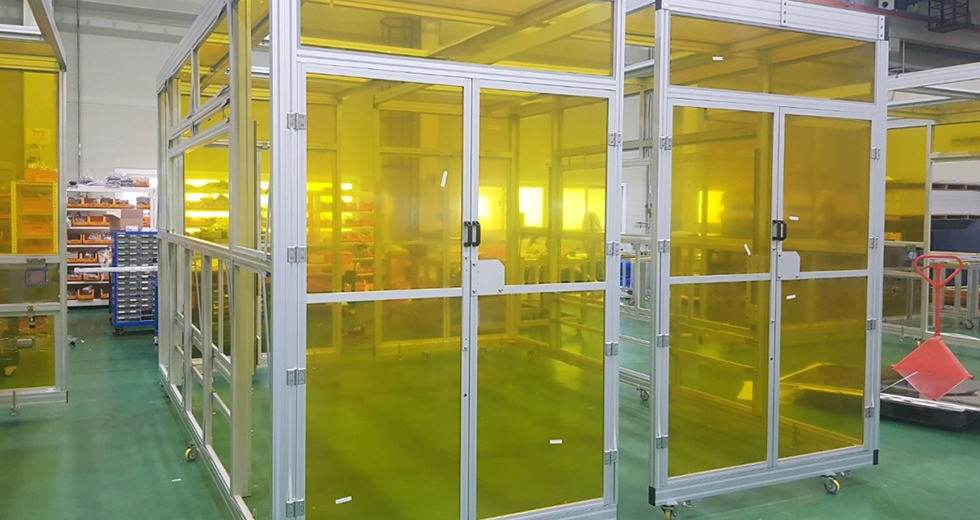
08 Quality Inspection
- Checking the product's quality and cleaning condition.
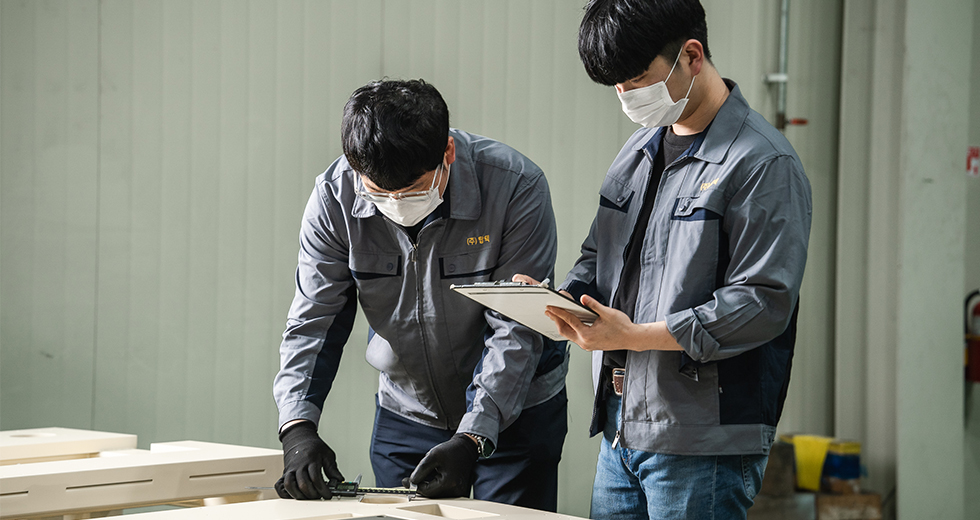